We have strong belief that is delivering optimized solution for customers’ needs meet.
- At first we discuss what is the main purposes for customers keeping up. After enough discussion, we fully reflect them while we carry out pilot test for customers’ product. We care for not only a process unit equipment but also whole process and auxiliary equipment. We can handle customers’ whole process plant design. Besides we also handle consigned processing for product sample check.
-
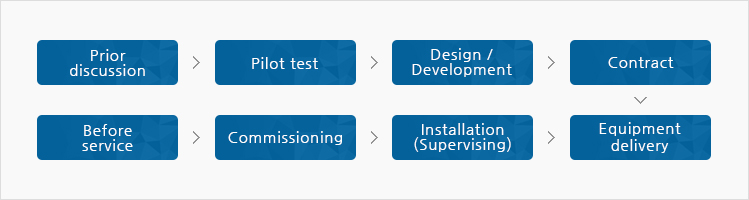